www.revista-fabricacion.com
15
'24
Written on Modified on
Yamaha: Aumento del rendimiento de montaje SMT con actualizaciones de uno o dos carriles
Comprender la verdadera ubicación de los cuellos de botella en las líneas SMT ayuda a los fabricantes a invertir de forma inteligente cuando llega el momento de actualizarlos.
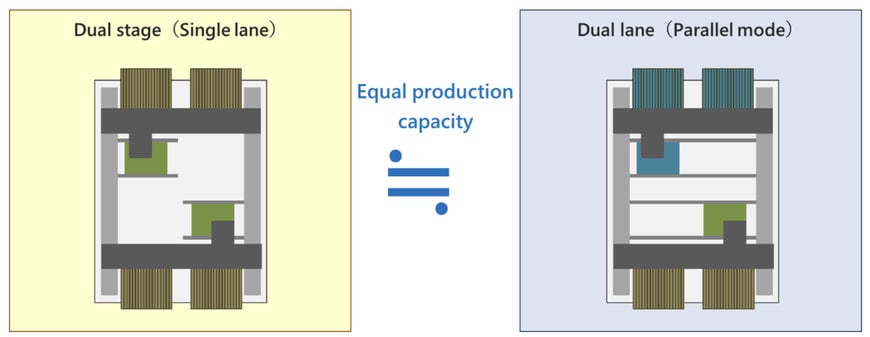
En la búsqueda de una mayor productividad, cualquier línea de montaje superficial puede contener un cuello de botella que suponga una barrera para aumentar el rendimiento. Añadir un montaje SMT adicional es una forma obvia de superarlo, aunque una máquina más rápida es otra opción. Por otra parte, podría ser el momento de actualizar la línea una configuración de doble carril.
La decisión óptima puede depender del tiempo de ciclo típico de la placa y de la variedad de componentes que se coloquen en cada PCB. Además, la eliminación del cuello de botella de la colocación pondrá de manifiesto las limitaciones de otros equipos de la línea, como el horno de reflujo. Por tanto, la respuesta a esta necesidad inmediata de velocidad debe ser sensible a los planes de inversión futuros de la fábrica.
Más montaje SMT
La incorporación de un montaje SMT adicional en la línea introduce una capacidad de colocación adicional, aunque la mejora puede ser menor de lo esperado. Un par de montajes SMT colocados en la línea amplía la distancia efectiva que cada placa debe recorrer para llegar al siguiente proceso, lo que aumenta las pérdidas totales de transferencia de PCB. La incorporación del montaje SMT adicional también aumenta el espacio total de la línea en una unidad adicional, lo que puede ser un problema si el espacio disponible es limitado.
Línea de doble carril
Para obtener un mayor rendimiento de la línea en un espacio limitado, cambiar a una línea de doble carril puede ofrecer ventajas. Con dos carriles y dos cabezales de colocación, un montaje SMT de dos haces y dos carriles puede duplicar matemáticamente la capacidad de colocación de la línea. En la práctica, sin embargo, el aumento de rendimiento puede ser menor. Además, se necesitan dos unidades de desplazamiento: una para transferir placas desde una serigrafía de un solo carril a un montaje SMT de doble carril y otra para transferir placas pobladas desde montaje SMT al horno de reflujo.
El montaje SMT de doble carril puede utilizarse en dos modos. En el modo paralelo, se cargan dos placas simultáneamente y se rellenan al mismo tiempo, ya que los dos cabezales de colocación funcionan de forma independiente. El tiempo de transferencia, para introducir las placas en el montaje SMT y aplicar las herramientas listas para la colocación de los componentes, debe tenerse en cuenta al calcular el tiempo total del ciclo. Cuando se trabaja en modo paralelo, sólo se puede utilizar un lado del banco de alimentación para cada línea de placas. Esto puede ser una desventaja cuando se construyen placas que tienen una gran mezcla de tipos de componentes.
Por otro lado, el montaje SMT puede funcionar en modo alterno. En este caso, la placa de un carril se rellena mientras que el segundo carril se encarga de transferir y fijar la siguiente placa. De este modo, el tiempo de transferencia de la tarjeta se reduce a cero. Sin embargo, los dos cabezales no pueden funcionar continuamente, ya que cada uno debe esperar para evitar interferencias con el otro.
Comparar el rendimiento
Teniendo en cuenta que el tiempo típico de transferencia de una placa suele ser de unos dos o tres segundos, el modo alternativo puede conseguir un tiempo de ciclo más rápido cuando hay que colocar un número reducido de componentes. Es entonces cuando el ahorro del tiempo de transferencia de la placa tiene el impacto más significativo en la reducción del tiempo total del ciclo.
A medida que aumenta el número de componentes que hay que montar, el tiempo dedicado a colocar componentes representa una proporción mayor del tiempo de ciclo. En consecuencia, la ventaja de ahorrar el tiempo de transferencia en modo alternativo disminuye. En la práctica, si el tiempo de ciclo es superior a unos 15 segundos, las pérdidas acumuladas en modo alterno mientras cualquiera de los cabezales no está realizando trabajo para evitar interferencias entre cabezales superan el ahorro conseguido al anular el tiempo de transferencia de la placa. Si este es el caso, el modo paralelo puede ofrecer una mayor productividad, siempre que se disponga de un acceso adecuado al alimentador.
Otro modo
A pesar de la mejora potencial de la velocidad en cualquiera de los modos, un montaje SMTE de doble carril puede no ser la mejor solución para una línea de un sólo carril. En la práctica, la capacidad de producción de montaje SMT no viene determinada por el número de carriles, sino por la utilización del cabezal de colocación. La mayor productividad depende de mantener activos los cabezales de colocación durante la mayor parte posible del tiempo de ciclo.
Teniendo esto en cuenta, un montaje SMT de un carril y dos etapas con dos cabezales de colocación puede tener la misma capacidad teórica que una máquina de dos vías en modo paralelo (figura 1), al tiempo que permite el acceso a los alimentadores delantero y trasero.
Las pérdidas de transferencia de placas incluyen el tiempo extra para la división de carriles, que se realiza dentro del montaje SMT. Por otro lado, no se necesita ninguna unidad de desplazamiento para sacar las placas de la serigrafía. El tiempo de espera para evitar la interferencia del cabezal es nulo y el tamaño compacto equivalente al de un montaje SMT de un solo carril garantiza que la distancia total recorrida para recoger y colocar sea corta.
En general, si no hay condiciones especiales relacionadas con el tipo de placas que se montan, un montaje SMT de dos fases y dos cabezales puede aumentar la productividad de forma más eficaz que introducir una montaje SMT de doble carril o dos máquinas convencionales de un solo cabezal.
Comprender el cuello de botella
Cuando el montaje de componentes es el proceso que restringe el rendimiento de la línea, la respuesta adecuada es aumentar la capacidad de montaje. Sin embargo, si el cuello de botella se debe a otro proceso, aumentar el rendimiento de la colocación de componentes puede ser una inversión inútil. Para ilustrar este punto, consideremos una línea SMT como la de la figura 2, con los tiempos de ciclo de proceso que se muestran. En este caso, el primer montaje SMT es el cuello de botella y limita el tiempo de ciclo de la línea a 40 segundos.
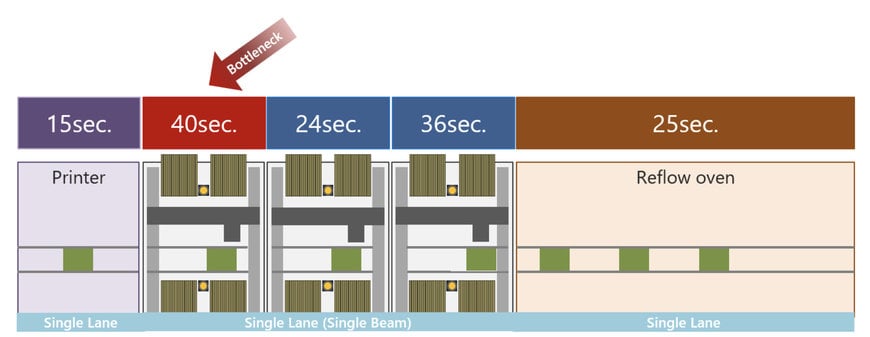
La máquina de montaje limita el rendimiento de la línea SMT.
Evitar montajes SMT inactivos
En el ejemplo de la figura 3, la actualización a doble etapa de un solo carril ha reducido el tiempo de montaje y el proceso de soldadura por reflujo define ahora el tiempo de ciclo de la línea. Este tiempo no puede reducirse, porque el perfil de reflujo tiene una duración fija. En la ilustración, cada montaje SMT es significativamente más rápido que el tiempo de ciclo limitado por el reflujo y está inactivo durante varios segundos por ciclo. La inversión en velocidad de montaje se desperdicia.
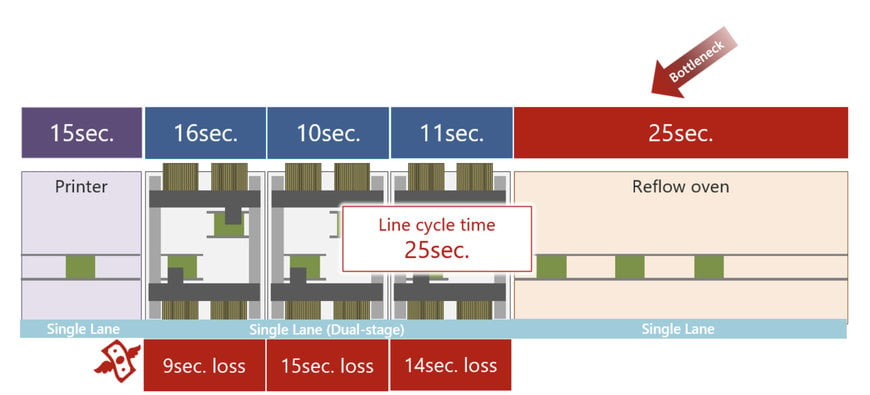
El proceso de reflujo limita el tiempo de ciclo de la línea SMT.
Un tiempo de ciclo efectivo de 25 segundos es bastante típico para la soldadura por reflujo. Si el montaje SMT de la línea y es más rápido que esto, el proceso de reflujo es el cuello de botella más probable.
La mejora del proceso de reflujo de un carril con un horno de doble carril reduce el tiempo de ciclo a 12,5 segundos, como muestra la figura 4. En este caso, el proceso de soldadura de componentes de doble carril es más rápido. En este caso, el montaje SMT de componentes de doble carril puede interactuar eficazmente con el horno de reflujo. Se necesita una unidad de desplazamiento entre la serigrafía de un carril y el montaje SMT de doble carril.
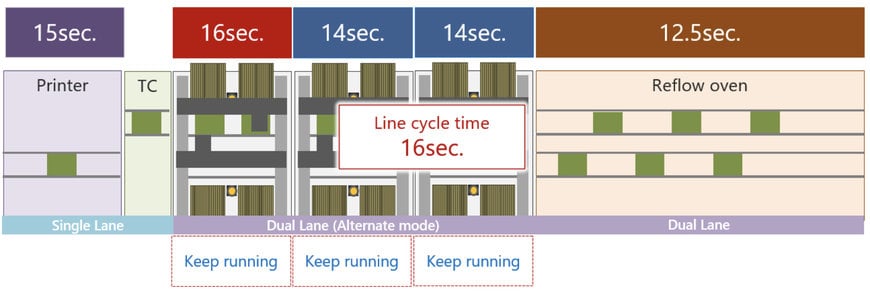
El tiempo de ciclo más rápido con reflujo de doble carril y montaje de componentes. Se utilizan todos los cabezales del montaje SMT.
El más largo de los procesos de montaje define el tiempo de ciclo global de la línea. Aunque este montaje SMT está limitando de hecho el rendimiento de la línea, el tiempo de ciclo ha mejorado significativamente en comparación con el ejemplo de la figura 1 y todos los cabezales de montaje se utilizan plenamente; por tanto, en este ejemplo no se está desperdiciando ninguna inversión en rendimiento de montaje.
Un montaje SMT de un solo carril y dos etapas, como se muestra en la figura 3, puede llevar las placas a un reflujo de dos carriles utilizando una unidad transversal y también permite un tiempo de ciclo más rápido que una configuración de dos carriles. La máquina de doble etapa también ofrece la flexibilidad de volver a la operación de una sola etapa para rellenar placas más pequeñas que tienen un tiempo de ciclo más corto. Una herramienta de software como el optimizador de línea de Yamaha puede calcular y aplicar automáticamente los ajustes más eficaces. La tabla resume las opciones típicas para los responsables de SMT que buscan mejorar el tiempo de ciclo de sus líneas.
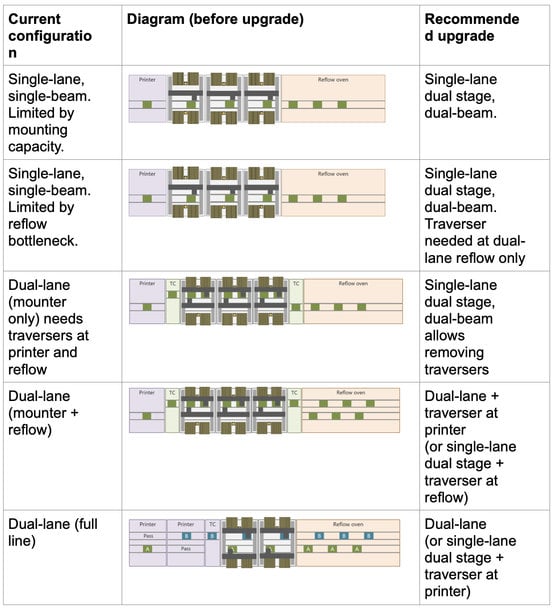
Directrices para la mejora del tiempo de ciclo.
Conclusión
Toda línea SMT contiene un cuello de botella. Cuando llega el momento de actualizar, comprender su ubicación es vital para dirigir la inversión de forma adecuada. Cuando el tiempo de ciclo de montaje es largo, la colocación en dos etapas es una opción sólida. Cuando el tiempo de ciclo es corto, invertir en reflujo de doble carril puede ser más eficaz.
La introducción de la automatización de doble carril en una línea de un solo carril no es una actualización sencilla y conlleva compromisos en cuanto al rendimiento y la disponibilidad del alimentador. Si el espacio es limitado y hay que mantener otros equipos de un solo carril, un montaje SMT de un solo carril de doble etapa puede aumentar la productividad de forma cómoda y rentable.
www.yamaha-motor-robotics.com