www.revista-fabricacion.com
25
'21
Written on Modified on
LA PRECISIÓN IMPORTA: LA EMPRESA CORE SENSING GMBH SE APOYA EN LA EXPERIENCIA DE HBK PARA DESARROLLAR UN EJE DE TRANSMISIÓN SENSORIZADO
Los componentes móviles de las máquinas y los vehículos comerciales deben soportar cargas pesadas a diario. Además, a menudo trabajan en condiciones difíciles. Como resultado, sufren desgaste y se deterioran, hasta el punto de ocasionar tiempos de inactividad que siempre son costosos. En el contexto del internet industrial de las cosas y los conceptos de Industria 4.0, el mantenimiento predictivo puede ayudar a minimizar esas averías.
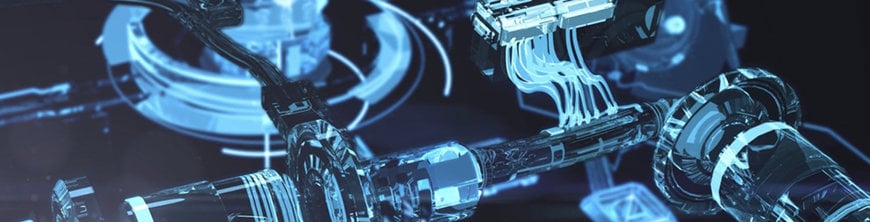
Las estrategias de mantenimiento preventivo están orientadas a vigilar el estado de los equipos y trabajan con previsiones. La empresa core sensing GmbH desarrolla soluciones que proporcionan en tiempo real datos sobre el estado de las máquinas y las plantas, imprescindibles para predecir cuál es el momento oportuno para cada intervención de mantenimiento. Para ello se requiere tecnología de medición innovadora, capaz de proporcionar información muy fiable de lo que ocurre en el interior de los componentes.
core sensing GmbH ha encontrado en HBK a un socio experimentado. En concreto, la experiencia del equipo de sensores OEM de HBK ha sido muy valiosa para desarrollar con éxito un eje de transmisión sensorizado inteligente.
Desafío
Con frecuencia, el mantenimiento que se hace de la maquinaria, los equipos y los vehículos comerciales no tiene en cuenta qué labores de mantenimiento se requieren realmente. A menudo, cuando se detectan los problemas ya es demasiado tarde. Eso, si llegan a detectarse. Las consecuencias son evidentes: tiempos de inactividad que salen caros y pérdida de actividad.
Solución
La empresa core sensing ha conseguido integrar sensores en un eje de transmisión, con el fin de monitorizarlo. HBK ha colaborado en el desarrollo de los sensores, que utilizan tecnología de galgas extensométricas de alta fiabilidad. Estos sensores proporcionan datos valiosos en tiempo real, muy útiles para predecir con precisión el estado del eje y los componentes adyacentes. Con ello, a su vez, se pueden planificar programas de mantenimiento adecuados y reparaciones en el momento oportuno.
Resultado
Los sensores de core sensing, integrados en un eje de transmisión sensorizado inteligente, permiten determinar los momentos más idóneos para el mantenimiento. El mantenimiento predictivo resultante evita averías costosas. Para implantar estos sensores inteligentes, la empresa ha colaborado estrechamente con HBK.
Averías costosas, a pesar del mantenimiento regular
Las plantas, las máquinas y los vehículos comerciales se someten a grandes tensiones a diario. Para garantizar que estén siempre funcionales, las empresas llevan a cabo un mantenimiento periódico. Sin embargo, con frecuencia se desconoce cuál es el estado real de los equipos y, por tanto, qué mantenimiento necesitan realmente. Por otro lado, a menudo no se detectan determinados puntos de desgaste potencial de los componentes, lo que propicia que aparezcan problemas entre inspección e inspección.
Incluso aunque el mantenimiento sea cuidadoso, siguen apareciendo problemas en las plantas, las máquinas y los vehículos comerciales, que provocan averías y tiempos de inactividad costosos. Por regla general, solo se investigan las causas raíz cuando se produce un fallo. Igualmente, no se piden las piezas de repuesto necesarias hasta que se produce un fallo. Esto da lugar a tiempos de espera innecesarios y a pérdidas de producción que salen muy caras.
Sin embargo, la digitalización y los conceptos de Industria 4.0, pueden poner remedio a estos problemas. La clave está en dotar de inteligencia a los componentes más importantes de las máquinas, como los ejes de transmisión o los acoplamientos, de modo que envíen regularmente feedback a los usuarios informando de su estado. Eso es justamente lo que hace el eje de transmisión sensorizado inteligente de Elbe Group, que incorpora sensores inteligentes de core sensing.
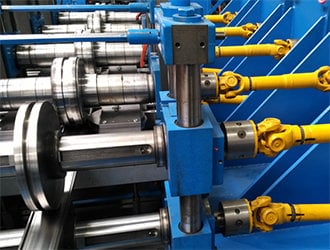
Componentes sensorizados innovadores: la revolución
Muchas máquinas y vehículos comerciales montan ejes de cardán que se someten a grandes cargas, sobre todo si el entorno es difícil. A medida que pasa el tiempo, aumenta la probabilidad de que el eje de transmisión se deteriore por fatiga y desgaste de los materiales, acarreando paradas de la máquina. Sin embargo, la información en tiempo real sobre el estado actual del componente ayuda a identificar posibles problemas y permite actuar para evitar averías costosas.
El líder del mercado, el Grupo Elbe, en colaboración con core sensing, ha desarrollado una innovadora familia de ejes de transmisión sensorizados. Estos componentes inteligentes envían continuamente datos sobre su estado. De este modo, es posible detectar y corregir oportunamente problemas potenciales. Las paradas con incidencias importantes en los costes se reducen notablemente. Se puede decir que, con esto, se ha hecho realidad una aspiración de muchos fabricantes de plantas y vehículos.
Un eje de transmisión con tecnología de medida inteligente
core sensing ha desarrollado un eje de transmisión de nueva generación con inteligencia integrada. Para ello, ha incorporado sensores inteligentes y electrónica de medición en la cavidad ya existente en el eje, que proporciona la mejor protección posible. El sensor queda estructuralmente integrado y transmite datos de par precisos y en tiempo real desde el eje de transmisión. Con estos datos, se pueden extraer conclusiones fiables sobre el estado del eje y los componentes cercanos.
HBK se encargó de personalizar y suministrar galgas extensométricas de torsión y de fuerza, para medir el par y la fuerza en el eje de transmisión. Para ello, las galgas extensométricas se adaptaron de forma óptima a las condiciones ambientales de la aplicación: geometría, tamaño, materiales y compensación de temperatura. Los usuarios reciben datos precisos y fiables de par y fuerza axial, que se complementan con otras variables adicionales que obtiene el conjunto de la cadena de medida con la ayuda de las soluciones inteligentes de core sensing. Los datos se transmiten de forma inalámbrica desde los sensores a un gateway o a la aplicación Core Viewer mediante una conexión estándar de 2,4 GHz. Esta tecnología de medición que va instalada en el eje de transmisión destaca por su eficiencia energética y recibe alimentación de una batería con autonomía para varios meses.
Pequeños y eficaces, para reducir los costes
El eje de transmisión sensorizado inteligente de Elbe Group con los sensores desarrollados por core sensing y HBK aporta numerosas ventajas, ya que el uso de un componente inteligente se traduce en reducciones de costes.
A efectos de mantenimiento predictivo, este eje sensorizado puede integrarse directamente en la trayectoria de carga de una cadena cinemática, para medir las cargas reales que se producen durante el funcionamiento. Los valores obtenidos en condiciones reales se comparan con valores de referencia previamente establecidos. De este modo se lleva a cabo una monitorización fiable del estado del eje de transmisión.
Y no solo eso: el hecho de situar un elemento sensor en la cadena cinemática proporciona información valiosa sobre el conjunto de la máquina. Si se selecciona bien el punto de medición, se pueden registrar las cargas que actúan sobre otros componentes y determinar su grado de deterioro.
La información sobre las variables de carga reales permite determinar —con un solo sensor— tanto la vida útil restante del eje de transmisión y los componentes cercanos como el momento más idóneo para las labores de mantenimiento predictivo. De mismo modo, se pueden predecir de manera fiable las posibles averías, utilizando algoritmos inteligentes basados en aprendizaje automático. Como resultado, se evitan los tiempos de inactividad costosos y se obtienen ahorros de costes sustanciales.
Otra fuente importante de reducción de costes es la monitorización de estado a partir de los datos del sensor. Lo más interesante es que favorece un funcionamiento más seguro y proporciona información relevante sobre la eficiencia de la máquina. A partir de esa información se puede optimizar el consumo de energía (un recurso siempre valioso) sin reducir el rendimiento de la máquina.
www.hbm.com