www.revista-fabricacion.com
17
'19
Written on Modified on
Una aproximación sistemática al portaherramientas ideal
Las modernas máquinas multitarea de cinco ejes y los centros de mecanizado de alta precisión para el microcorte, permiten implementar conceptos de mecanizado constantemente nuevos y mejorados.
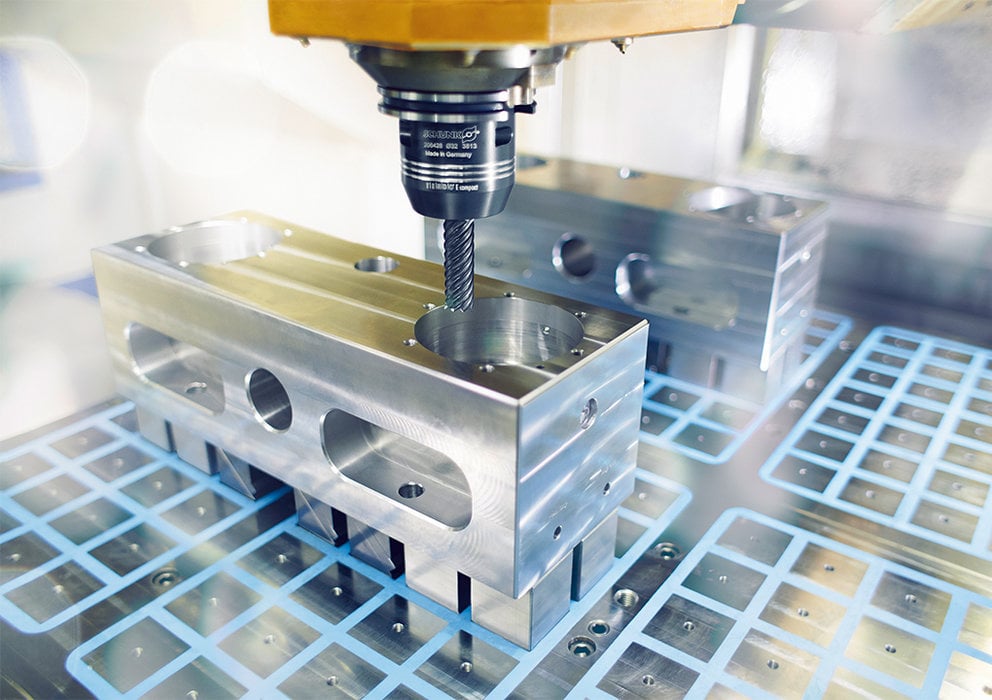
Las diferentes necesidades de los distintos sectores se reflejan en la distribución de sistemas portaherramientas en todo el mundo. Mientras que alrededor del 60% de estos sistemas en Europa son mandriles térmicos, la proporción correspondiente en EE. UU. y Asia es del 20% y 30% respectivamente.
Los portapinzas, por otro lado, desempeñan un papel mucho más importante fuera de Europa que en Alemania. La proporción de chucks de expansión hidráulica de alta precisión, a su vez, se sitúa entre el 8 % y el 15 % en todo el mundo. A la hora de evaluar la evolución del mercado de los sistemas portaherramientas, adquieren importancia dos aspectos principales: en primer lugar, la diversidad de variantes es cada vez mayor.
Por otro lado, los soportes de precisión están ganando importancia rápidamente, ya que la mejora de la calidad y el rendimiento de las herramientas mecánicas hace que aumente la demanda de fiabilidad del proceso y la vida útil de las herramientas. Además, el aumento de la eficiencia en la producción de portaherramientas de precisión reduce significativamente el coste en comparación con los mandriles mecánicos, tales como Weldon, Whistle-Notch o sistemas de collet chuck.
Sobre todo en el caso de los chucks de expansión hidráulica, los precios iniciales han bajado considerablemente. Esto hace que sea aún más importante cuestionar las estrategias establecidas para los portaherramientas de forma regular, especialmente cuando se invierte en nuevas herramientas mecánicas.
Una evaluación del sistema global
Si comparamos los sistemas portaherramientas individuales, sus características técnicas y sus interfaces con el husillo de la máquina, resulta evidente que no existe un sistema portaherramientas óptimo para todas las aplicaciones. La selección de un sistema es siempre una decisión única que depende de una variedad de parámetros.
El portaherramientas no debe considerarse una pieza aislada, sino que siempre debe incluirse dentro de la interacción del conjunto del sistema (formado por la sujeción pieza, la pieza, la herramienta, el portaherramientas, la interfaz del husillo y la máquina).
Como interfaz principal con la pieza de trabajo, el portaherramientas desempeña un papel esencial, entre otros, porque es capaz de compensar parcialmente las debilidades del sistema global.
La selección del sistema portaherramientas ideal debe realizarse gradualmente en varios pasos. En primer lugar, es importante definir los criterios básicos que influyen significativamente en la estabilidad subyacente del proceso. Estos incluyen la fuerza de sujeción requerida, la rigidez radial, el contorno de interferencia y, si procede, la idoneidad para aplicaciones de alta velocidad.
En un segundo paso, el enfoque se centra en los criterios de calidad que afectan a la calidad del proceso, la precisión y la productividad. Entre ellos, se incluyen la precisión de excentricidad y de repetición, la calidad de equilibrado, la amortiguación de vibraciones, el suministro de refrigerante y la posibilidad de preajustar la longitud.
Por último, en la tercera etapa, es aconsejable considerar criterios económicos en el marco de un análisis de coste-beneficio (es decir, los costes de adquisición, la vida útil, la flexibilidad y la reutilización, así como los costes del funcionamiento continuado).
Los criterios básicos son vitales para la estabilidad del proceso
Los criterios básicos para la selección del portaherramientas pueden entenderse como criterios de exclusión. Deben cumplirse durante el proceso de mecanizado para poder continuar.
Fuerza/par de sujeción: la fuerza de sujeción del portaherramientas determina hasta qué punto se puede controlar el par en la interfaz entre el portaherramientas y la herramienta. Si la fuerza de sujeción es suficiente, el filo de corte de la herramienta encaja uniformemente en el material.
Si no es suficiente, la herramienta comenzará a girar en el soporte y el corte será inestable. En casos extremos, la herramienta se soltará por completo del portaherramientas. La transmisión de par se alcanza de diferentes maneras en los sistemas portaherramientas: las herramientas pueden enroscarse mediante roscas en el cuerpo.
En este caso, el diseño de la rosca debe corresponderse al menos con el par de salida. Una segunda variante son las herramientas de sujeción mecánica que están equipadas con un accionamiento positivo. Solo cuando los pares de torsión que se producen superan la resistencia a la rotura o al cizallamiento de los componentes, un apriete de este tipo fallaría.
Por regla general, estas resistencias son muy superiores a los pares de torsión que se producen durante el mecanizado, por lo que se garantiza una alta fiabilidad del proceso de uso de herramientas de sujeción mecánica. Por último, la tercera opción es la sujeción de herramientas por fuerza, la cual emplea conexiones de prensa cruzada.
En este caso, el agujero que sostiene la herramienta se ve influido por el calor o las fuerzas externas, por lo que la herramienta se tensa mediante un solapamiento. Por regla general, los sistemas portaherramientas de precisión, como los chucks de expansión hidráulica, funcionan de acuerdo con este principio.
En el contexto de los últimos desarrollos tecnológicos, ha sido posible aumentar las fuerzas de sujeción de los chucks de expansión hidráulica hasta tal punto que se puede lograr de manera fiable un mecanizado de volumen uniforme. Con un diámetro de 20 mm, los chucks de expansión hidráulica modernos transmiten pares de hasta 900 Nm.
Rigidez radial: la elevada rigidez radial permite fuerzas de corte superiores (es decir, avances y velocidades de avance grandes). Por tanto, es un criterio esencial para el mecanizado de volumen, ya que influye de manera decisiva en el tiempo de mecanizado y, a su vez, en la productividad, pero también en el la posible proyección de las herramientas.
La rigidez radial depende de las propiedades del material del portaherramientas (módulo E) y de su procesamiento, de la geometría del portaherramientas y de su integración en el sistema global de la herramienta mecánica, especialmente desde la interfaz hasta el husillo de la máquina.
En pocas palabras: cuanto más corto sea el portaherramientas, mayor será su diámetro, más homogénea será la unidad de herramienta y su soporte, más fuerte será la pared del soporte de la herramienta, más amplio será el apoyo del portaherramientas en el husillo y mayor será la rigidez radial.
Contorno de interferencia: si las piezas de trabajo en máquinas de cinco ejes modernas se mecanizan por completo en solo dos pasos de sujeción, la accesibilidad juega un papel esencial. Lo que se necesita son portaherramientas delgados que transmitan un par suficientemente alto y que, al mismo tiempo, garanticen una alta precisión en la pieza de trabajo.
En espacios especialmente estrechos, es posible utilizar extensiones de herramienta alternativas, las cuales pueden montarse entre la herramienta y el portaherramientas si es necesario. A diferencia de los portaherramientas de contorno optimizado con una interfaz de husillo, las extensiones de herramienta se pueden utilizar de forma muy flexible. Están disponibles con diferentes tecnologías de sujeción.
Idoneidad para alta velocidad: si las velocidades del husillo alcanzan 80 000 r. p. m. y más durante el corte a alta velocidad, los portaherramientas deben cumplir condiciones especiales en términos de geometría, concentricidad, calidad de equilibrado y fiabilidad del proceso durante el cambio de herramienta.
Cuanto menor sea el diámetro de sujeción, con mayor frecuencia alcanzarán sus límites los portaherramientas universales mecánicos, pero también los portaherramientas termorretráctiles o de expansión hidráulica, ya sea porque el espacio disponible no es suficiente para el mecanismo de sujeción correspondiente o porque las herramientas de dimensiones tan pequeñas ya no pueden sustituirse de forma fiable o ajustarse con precisión.
Otras tecnologías de sujeción, como la tecnología de sujeción poligonal, que no contiene piezas móviles, cobran aquí importancia.
Los criterios de calidad determinan la precisión y la productividad
Históricamente, el cumplimiento de los criterios básicos ha sido suficiente para realizar la mayoría de las operaciones de mecanizado. Debido a las crecientes exigencias en cuanto a la calidad de las piezas de trabajo y la eficacia del mecanizado, así como en el contexto de los conceptos y procedimientos modernos de herramientas mecánicas, factores que antes se consideraban secundarios y que también podrían describirse como criterios de calidad están adquiriendo cada vez más importancia.
Aquí también se observan velocidades de desarrollo diferentes según el sector y la región. Cuanto más altos sean los requisitos en cuanto a precisión dimensional, calidad de la superficie, pero también en cuanto a rentabilidad, más relevancia adquieren los siguientes criterios de calidad.
Precisión de excentricidad: para el mecanizado de precisión, la precisión de excentricidad de las herramientas y de toda la cadena de transmisión es de vital importancia. Determinan si se alcanzan las dimensiones y tolerancias. Además, la precisión de excentricidad influye de manera significativa en el desgaste del filo de la herramienta y en la vida útil del husillo de la máquina.
Si la herramienta sujetada no gira de forma céntrica respecto al eje del portaherramientas, existe el riesgo de que se produzcan imprecisiones y no se alcancen las dimensiones requeridas en la pieza de trabajo. Además, las herramientas comenzarán a golpear durante el mecanizado, lo que provoca microerosiones en la hoja y acelera el desgaste de la misma.
Precisión de repetición: la precisión de repetición de un portaherramientas describe lo bien que un portaherramientas puede reproducir un parámetro definido en varios intentos. Para el mecanizado de precisión moderno, lo decisivo no es la precisión absoluta, sino la repetibilidad de la máquina y, por tanto, del portaherramientas.
Los errores sistemáticos de la máquina pueden compensarse con relativa facilidad en las máquinas CNC modernas si se emplean algoritmos en el control de la máquina. Sin embargo, esto solo es posible si existe un alto grado de repetibilidad, es decir, si las desviaciones respectivas son siempre tan idénticas como sea posible.
Por tanto, la precisión de repetición del portaherramientas es decisiva para determinar qué precisiones se consiguen en última instancia en la pieza de trabajo.
Calidad de equilibrado: en términos sencillos, un desequilibrio surge cuando la masa en un cuerpo giratorio se distribuye de forma desigual, ya sea porque el centro de gravedad no está situado en el eje de rotación (desequilibrio estático) o porque el eje principal de inercia no es paralelo al eje de rotación (desequilibrio dinámico).
Los portaherramientas suelen tener una combinación de desequilibrio estático y dinámico. Las causas pueden incluir interpretaciones técnicas relacionadas con el diseño del portaherramientas o de la herramienta (por ejemplo, herramientas de un solo filo), el diseño asimétrico del portaherramientas (por ejemplo, debido a las ranuras de la pinza o a los tornillos de sujeción), la distribución asimétrica de la masa debido a tolerancias de fabricación, la desalineación o los errores en el montaje del cuerpo giratorio.
Los portaherramientas con grandes desequilibrios tienen efectos negativos en varios aspectos: menor calidad de la superficie debido a las vibraciones en el portaherramientas, velocidades de corte limitadas, menor precisión de producción, menor vida útil de la herramienta o daños en los cojinetes del husillo de la máquina.
Amortiguación de vibraciones: en función de la respuesta de frecuencia del sistema general que comprende la máquina, el portaherramientas, la herramienta, la sujeción de la pieza y la pieza, se producirán vibraciones durante los procesos de mecanizado. Estas pueden tener efectos considerables en el resultado del mecanizado y provocar un mayor desgaste de la herramienta, su rotura o daños en la máquina.
De forma similar a un amortiguador, los portaherramientas pueden amortiguar las vibraciones y permitir una acción de corte suave y constante, ello dependiendo de la tecnología de sujeción. Esto permite reducir las emisiones de ruido, mejorar la calidad de la superficie de la pieza de trabajo, prolongar la vida útil de la herramienta y proteger el husillo.
Suministro de refrigerante: los lubricantes refrigerantes realizan muchas funciones durante el mecanizado. Eliminan las virutas, reducen el calor y la fricción, garantizan una temperatura uniforme de la herramienta y de la pieza de trabajo y ayudan a cumplir las tolerancias.
Dependiendo del tipo de suministro de refrigerante, se puede distinguir entre refrigeración externa, refrigeración periférica y refrigeración interna. La refrigeración interna ofrece ventajas particulares: el lubricante refrigerante llega exactamente al borde de corte sin tener que alinear manualmente las boquillas del refrigerante, y las virutas también se eliminan de forma fiable en los contornos estrechos y profundos.
Incluso si hay que taladrar agujeros profundos, el borde de corte se puede enfriar de forma eficaz. Como resultado, la vida útil de la herramienta se prolonga y los parámetros del proceso a veces se incrementan significativamente.
Los criterios económicos influyen en la eficiencia del mecanizado
Mientras que los criterios básicos y los criterios de calidad definen directamente el proceso de mecanizado y siempre se consideran prioritarios, los criterios económicos ayudan a tomar una decisión final desde el punto de vista económico. Además de los costes de adquisición del portaherramientas, por un lado, hay que tener en cuenta los costes directos: vida útil, inversiones en periféricos, costes de funcionamiento (cambio de herramientas, limpieza, preajuste de longitud y mantenimiento), flexibilidad, consumo de energía durante el cambio de herramientas y reutilización de los soportes.
Por otra parte, los costes indirectos en particular desempeñan un papel clave. Estos incluyen, sobre todo, los costes de la herramienta (ya que la vida útil de las herramientas varía considerablemente en función del sistema de sujeción utilizado) y los costes/ahorros derivados de la reducción o el aumento de la productividad.
Desde el punto de vista de la vida útil, los costes indirectos por portaherramientas pueden suponer un ahorro de cinco cifras. Además, el aspecto de la prevención de accidentes ha ido ganando importancia rápidamente en los últimos tiempos. En particular, las quemaduras o los aplastamientos se consideran riesgos potenciales.
Comparación sistemática
El catálogo de criterios recomienda una consideración detallada de la aplicación correspondiente a la hora de seleccionar un portaherramientas. SCHUNK, como líder en sistemas y tecnología de sujeción, dispone de conocimientos especializados en este campo. Además, el programa de portaherramientas de SCHUNK está considerado como la gama tecnológica más completa fabricada en Alemania.
Abarca desde portaherramientas mecánicos y soportes de termorretracción hasta económicos portaherramientas de tensión hidráulica, pasando por chucks de alta gama basados en la expansión hidráulica o la tecnología de sujeción poligonal. El portaherramientas sensorial iTENDO es, ahora mismo, la más alta categoría, lo que hace posible una detección del estado y una documentación de la estabilidad del proceso impecables, un control de la velocidad y del avance en tiempo real, así como una detección del valor límite sin intervención humana.
www.schunk.com