www.revista-fabricacion.com
04
'11
Written on Modified on
Pruebas de motores eléctricos para aplicaciones de automoción
Para sus bancos de prueba utilizados tanto en laboratorios como en producción, Unus International escogió la solución llave en mano MEROBEL.
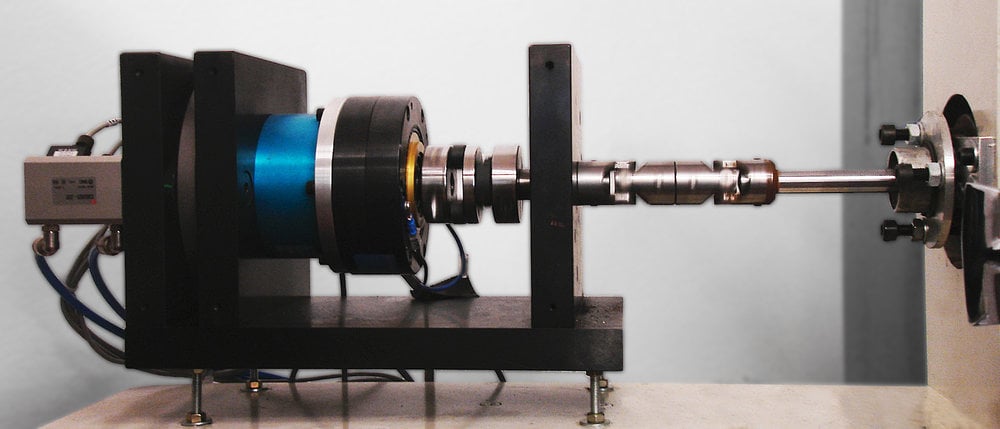
UNUS International fabrica motores CC de 12 – 24 - 48 V utilizados principalmente como equipos de servomecanismo para el sector de la automatización en la automoción y la industria.
UNUS, que fue creada en la década de 1970 en Padova y en 1995 se trasladó a Rival di Pianiga (Venecia), emplea actualmente a unas 60 personas y su producción supera las 2.000.000 piezas al año.
Esta producción incluye los siguientes motores y grupos reductores para el automóvil:
- Ventanas, techos solares, pantallas, mecanismos
- Movimiento y ajuste de los asientos
- Columna de dirección
- Caja de cambios automática
Su gama global de productos incluye asimismo otros equipos basados en motores y dirigidos a otros sectores industriales, como el control de puertas correderas, transmisión, puertas y automatización en general.
Los ingenieros de UNUS International están al servicio del cliente para el desarrollo de nuevos proyectos.
Los conocimientos técnicos y la flexibilidad son los principales valores de la compañía, pues permiten acortar el tiempo dedicado al diseño, prototipado y fabricación de las muestras iniciales de nuevos productos. Esta organización garantiza una rápida respuesta a la gran variedad de necesidades del mercado, con una gestión completa de los aspectos relacionados con el plazo de comercialización.
"Nuestra misión consiste en ofrecer un producto que se adapte a las necesidades del cliente, para lo cual el nivel técnico y la calidad son fundamentales", declaró Massimo Melato, Director General de Unus International. "En el punto de partida está nuestra política de calidad y nuestra I+D continuamente renovada, pero también el diseño, la producción y la organización del negocio en general, con el objetivo constante de mejorar la satisfacción del cliente”.
“Nuestros excelentes resultados, obtenidos en el mercado nacional e internacional con productos que contienen alta tecnología, confirman que estamos trabajando en la dirección correcta, al tiempo que mejoramos continuamente nuestra competitividad y nuestra calidad. Los motores y grupos reductores de UNUS son utilizados como primer equipamiento por los principales fabricantes alemanes de coches así como por los fabricantes más importantes de sistemas de automatización".
La importancia estratégica de las pruebas
Entre las razones de su éxito, junto con la capacidad tecnológica de la compañía, se encuentran los elevados niveles de fiabilidad y calidad de su producción.
UNUS International es una de las 100 compañías italianas de éxito que aparecen citadas en el 3º informe de Eurispes. Para asegurar este nivel de excelencia, las pruebas de los productos (durante la producción, pero también en el laboratorio durante el período de diseño), tienen una importancia absolutamente estratégica.
Se han instalado bancos de pruebas especializados para probar el 100% los motores dedicados a la industria de automoción. "Se emplean principalmente para ventanas motorizadas, movimiento de los asientos, apertura del techo, columna de dirección ajustable y transmisión de movimiento ", señala Massimo Melato. "En la actualidad estamos desarrollando un motor diseñado para funcionar como compresor para la suspensión neumática del coche.
Los bancos de pruebas no fueron diseñados para una aplicación de un cliente concreto. UNUS ha recopilado todas las especificaciones de numerosos fabricantes de coches y ha desarrollado unos bancos de pruebas versátiles y capaces de cumplir tales especificaciones.
"Las soluciones que se suelen encontrar en el mercado tratan generalmente de cubrir al abanico más amplio posible de aplicaciones", señala Massimo Melato, "pero por otro lado no cumplen totalmente las necesidades y las tareas específicas que se les exige. Al haber construido los bancos de pruebas en nuestra propia compañía y haber desarrollado su software de control hemos atendido nuestros requisitos o, mejor dicho, las necesidades reales de nuestros clientes".
En el proceso de fabricación se prueba cada motor, tanto en lo que respecta a los principales parámetros de funcionamiento como al nivel de ruido. "Para llevar a cabo las pruebas disponemos actualmente de 4 cabinas equipadas con frenos MEROBEL", indica Massimo Melato. "El ciclo de pruebas tiene una duración de 5 y 10 segundos, dependiendo del tipo de motor, con una producción diaria de unas 8.000 piezas".
Los otros bancos de prueba se encuentran en el laboratorio –donde 5 sistemas están equipados con frenos MEROBEL- con el fin de comprobar la fiabilidad de los motores y los grupos reductores mediante pruebas de vida operativa y de fatiga.
Para estos procesos la duración del ciclo de prueba es mucho mayor. Algunas pruebas de resistencia, con largos ciclos y simulación de envejecimiento por medio de ciclos de calor en una cámara climática, pueden durar hasta 60 días.
Existen por tanto dos aplicaciones muy diferentes entre sí.
"En el laboratorio, las pruebas se dedican principalmente a simular el ciclo de funcionamiento de los motores con diferentes ciclos de carga (p.ej., con diferentes niveles de par) y diferentes condiciones ambientales (como choques térmicos, rango de temperatura de -40 ° C a 90 ° C y diferentes valores de humedad relativa) para un cierto número de ciclos o hasta el fin de la vida operativa del motor", señala Massimo Melato. "Entonces utilizamos un ciclo de trabajo bien definido, en función de las especificaciones de los clientes". Durante la fase pruebas a los motores se monitoriza y registra constantemente cada parámetro (consumo de corriente, velocidad, par y temperatura).
Cuando el motor no cumple las exigencias o se produce un fallo (p.ej., un sobrecalentamiento, un desgaste prematuro de las escobillas o el fallo de algún componente), se deja a un lado para analizar las razones y para introducir las mejoras necesarias. Tras la modificación pertinente la prueba se repite por completo hasta lograr la calidad exigida al motor.
El único objetivo es que el motor cumpla todas las especificaciones del cliente y que una vez dentro de la fase de producción no haya que desechar ninguno.
Se aplica el mismo procedimiento una vez al año para las pruebas de los productos con el fin de comprobar que nada haya cambiado a lo largo del tiempo.
Frenos EMP robustos y fiables – Controladores de lazo cerrado de sencillo manejo
Para simular en los bancos de pruebas la carga variable que habrá de soportar el motor durante su vida operativa, Unus escogió una solución completa, basada en componentes MEROBEL, con la ayuda de la filial italiana de la compañía, ANDANTEX SpA.
Los componentes escogidos fueron los frenos EMP (tipo FAT120), sensor de par (tipo TRS50) y un controlador de lazo cerrado (tipo DGT300).
"ANDANTEX nos aconsejó que utilizáramos los frenos MEROBEL en esta aplicación así como el ajuste de la unidad de control y de varios parámetros en función de nuestras especificaciones”, dice Massimo Melato. "Se estableció una estrecha colaboración con ANDANTEX en el suministro de los frenos para todo el desarrollo de la aplicación. En concreto fue primordial compartir los avanzados conocimientos técnicos especializados con nuestros diseñadores de software a medida para obtener los sistemas de prueba final que cubrieran totalmente nuestras necesidades".
Entre la amplia gama de soluciones que ofrece MEROBEL se encuentran accionadores de alta tecnología como frenos y embragues EMP, controladores digitales, sensores y transductores. La especialización lograda por la compañía permite ofrecer soluciones óptimas para prácticamente cualquier tipo de sistema con aplicación de par variable, en función de sus requisitos específicos.
La gama de frenos y embragues MEROBEL EMP (ElectroMagnetic Particles) está formada por dos rotores concéntricos, exterior e interior, separados por un hueco en el que se encuentran las partículas magnéticas.
La variación del campo magnético en el hueco (creado por una bobina que genera una corriente CC variable) genera una “fluidez” variable de la partícula magnética que permite un acoplamiento mecánico suave y variable entre los dos rotores (par variable).
Esta tecnología especial garantiza un par estable, reproducible e independiente respecto a la velocidad de rotación y fácilmente ajustable con una pequeña corriente CC.
Entre las principales características de los frenos y embragues MEROBEL EMP está la proporcionalidad entre la corriente aplicada y el par suministrado, la independencia entre par y velocidad, su funcionamiento bidireccional, un desgaste muy pequeño y un funcionamiento silencioso.
Además, los frenos y embragues MEROBEL EMP ofrecen un bajo mantenimiento, rápido tiempo de respuesta (10 a 50 ms), bajo consumo eléctrico, respuesta lineal, funciones de control remoto muy sencillo y una fácil integración en todo tipo de sistemas de prueba.
"Estamos muy satisfechos con los productos MEROBEL y el soporte de ANDANTEX", concluyó Massimo Melato. "En un principio instalamos los frenos MEROBEL en los bancos de prueba para producción. E incluso si el nivel de exigencia fuera bastante mayor, ahora hemos ampliado el uso de estos frenos a los bancos de prueba de laboratorio con gran éxito”.
UNUS, que fue creada en la década de 1970 en Padova y en 1995 se trasladó a Rival di Pianiga (Venecia), emplea actualmente a unas 60 personas y su producción supera las 2.000.000 piezas al año.
Esta producción incluye los siguientes motores y grupos reductores para el automóvil:
- Ventanas, techos solares, pantallas, mecanismos
- Movimiento y ajuste de los asientos
- Columna de dirección
- Caja de cambios automática
Su gama global de productos incluye asimismo otros equipos basados en motores y dirigidos a otros sectores industriales, como el control de puertas correderas, transmisión, puertas y automatización en general.
Los ingenieros de UNUS International están al servicio del cliente para el desarrollo de nuevos proyectos.
Los conocimientos técnicos y la flexibilidad son los principales valores de la compañía, pues permiten acortar el tiempo dedicado al diseño, prototipado y fabricación de las muestras iniciales de nuevos productos. Esta organización garantiza una rápida respuesta a la gran variedad de necesidades del mercado, con una gestión completa de los aspectos relacionados con el plazo de comercialización.
"Nuestra misión consiste en ofrecer un producto que se adapte a las necesidades del cliente, para lo cual el nivel técnico y la calidad son fundamentales", declaró Massimo Melato, Director General de Unus International. "En el punto de partida está nuestra política de calidad y nuestra I+D continuamente renovada, pero también el diseño, la producción y la organización del negocio en general, con el objetivo constante de mejorar la satisfacción del cliente”.
“Nuestros excelentes resultados, obtenidos en el mercado nacional e internacional con productos que contienen alta tecnología, confirman que estamos trabajando en la dirección correcta, al tiempo que mejoramos continuamente nuestra competitividad y nuestra calidad. Los motores y grupos reductores de UNUS son utilizados como primer equipamiento por los principales fabricantes alemanes de coches así como por los fabricantes más importantes de sistemas de automatización".
La importancia estratégica de las pruebas
Entre las razones de su éxito, junto con la capacidad tecnológica de la compañía, se encuentran los elevados niveles de fiabilidad y calidad de su producción.
UNUS International es una de las 100 compañías italianas de éxito que aparecen citadas en el 3º informe de Eurispes. Para asegurar este nivel de excelencia, las pruebas de los productos (durante la producción, pero también en el laboratorio durante el período de diseño), tienen una importancia absolutamente estratégica.
Se han instalado bancos de pruebas especializados para probar el 100% los motores dedicados a la industria de automoción. "Se emplean principalmente para ventanas motorizadas, movimiento de los asientos, apertura del techo, columna de dirección ajustable y transmisión de movimiento ", señala Massimo Melato. "En la actualidad estamos desarrollando un motor diseñado para funcionar como compresor para la suspensión neumática del coche.
Los bancos de pruebas no fueron diseñados para una aplicación de un cliente concreto. UNUS ha recopilado todas las especificaciones de numerosos fabricantes de coches y ha desarrollado unos bancos de pruebas versátiles y capaces de cumplir tales especificaciones.
"Las soluciones que se suelen encontrar en el mercado tratan generalmente de cubrir al abanico más amplio posible de aplicaciones", señala Massimo Melato, "pero por otro lado no cumplen totalmente las necesidades y las tareas específicas que se les exige. Al haber construido los bancos de pruebas en nuestra propia compañía y haber desarrollado su software de control hemos atendido nuestros requisitos o, mejor dicho, las necesidades reales de nuestros clientes".
En el proceso de fabricación se prueba cada motor, tanto en lo que respecta a los principales parámetros de funcionamiento como al nivel de ruido. "Para llevar a cabo las pruebas disponemos actualmente de 4 cabinas equipadas con frenos MEROBEL", indica Massimo Melato. "El ciclo de pruebas tiene una duración de 5 y 10 segundos, dependiendo del tipo de motor, con una producción diaria de unas 8.000 piezas".
Los otros bancos de prueba se encuentran en el laboratorio –donde 5 sistemas están equipados con frenos MEROBEL- con el fin de comprobar la fiabilidad de los motores y los grupos reductores mediante pruebas de vida operativa y de fatiga.
Para estos procesos la duración del ciclo de prueba es mucho mayor. Algunas pruebas de resistencia, con largos ciclos y simulación de envejecimiento por medio de ciclos de calor en una cámara climática, pueden durar hasta 60 días.
Existen por tanto dos aplicaciones muy diferentes entre sí.
"En el laboratorio, las pruebas se dedican principalmente a simular el ciclo de funcionamiento de los motores con diferentes ciclos de carga (p.ej., con diferentes niveles de par) y diferentes condiciones ambientales (como choques térmicos, rango de temperatura de -40 ° C a 90 ° C y diferentes valores de humedad relativa) para un cierto número de ciclos o hasta el fin de la vida operativa del motor", señala Massimo Melato. "Entonces utilizamos un ciclo de trabajo bien definido, en función de las especificaciones de los clientes". Durante la fase pruebas a los motores se monitoriza y registra constantemente cada parámetro (consumo de corriente, velocidad, par y temperatura).
Cuando el motor no cumple las exigencias o se produce un fallo (p.ej., un sobrecalentamiento, un desgaste prematuro de las escobillas o el fallo de algún componente), se deja a un lado para analizar las razones y para introducir las mejoras necesarias. Tras la modificación pertinente la prueba se repite por completo hasta lograr la calidad exigida al motor.
El único objetivo es que el motor cumpla todas las especificaciones del cliente y que una vez dentro de la fase de producción no haya que desechar ninguno.
Se aplica el mismo procedimiento una vez al año para las pruebas de los productos con el fin de comprobar que nada haya cambiado a lo largo del tiempo.
Frenos EMP robustos y fiables – Controladores de lazo cerrado de sencillo manejo
Para simular en los bancos de pruebas la carga variable que habrá de soportar el motor durante su vida operativa, Unus escogió una solución completa, basada en componentes MEROBEL, con la ayuda de la filial italiana de la compañía, ANDANTEX SpA.
Los componentes escogidos fueron los frenos EMP (tipo FAT120), sensor de par (tipo TRS50) y un controlador de lazo cerrado (tipo DGT300).
"ANDANTEX nos aconsejó que utilizáramos los frenos MEROBEL en esta aplicación así como el ajuste de la unidad de control y de varios parámetros en función de nuestras especificaciones”, dice Massimo Melato. "Se estableció una estrecha colaboración con ANDANTEX en el suministro de los frenos para todo el desarrollo de la aplicación. En concreto fue primordial compartir los avanzados conocimientos técnicos especializados con nuestros diseñadores de software a medida para obtener los sistemas de prueba final que cubrieran totalmente nuestras necesidades".
Entre la amplia gama de soluciones que ofrece MEROBEL se encuentran accionadores de alta tecnología como frenos y embragues EMP, controladores digitales, sensores y transductores. La especialización lograda por la compañía permite ofrecer soluciones óptimas para prácticamente cualquier tipo de sistema con aplicación de par variable, en función de sus requisitos específicos.
La gama de frenos y embragues MEROBEL EMP (ElectroMagnetic Particles) está formada por dos rotores concéntricos, exterior e interior, separados por un hueco en el que se encuentran las partículas magnéticas.
La variación del campo magnético en el hueco (creado por una bobina que genera una corriente CC variable) genera una “fluidez” variable de la partícula magnética que permite un acoplamiento mecánico suave y variable entre los dos rotores (par variable).
Esta tecnología especial garantiza un par estable, reproducible e independiente respecto a la velocidad de rotación y fácilmente ajustable con una pequeña corriente CC.
Entre las principales características de los frenos y embragues MEROBEL EMP está la proporcionalidad entre la corriente aplicada y el par suministrado, la independencia entre par y velocidad, su funcionamiento bidireccional, un desgaste muy pequeño y un funcionamiento silencioso.
Además, los frenos y embragues MEROBEL EMP ofrecen un bajo mantenimiento, rápido tiempo de respuesta (10 a 50 ms), bajo consumo eléctrico, respuesta lineal, funciones de control remoto muy sencillo y una fácil integración en todo tipo de sistemas de prueba.
"Estamos muy satisfechos con los productos MEROBEL y el soporte de ANDANTEX", concluyó Massimo Melato. "En un principio instalamos los frenos MEROBEL en los bancos de prueba para producción. E incluso si el nivel de exigencia fuera bastante mayor, ahora hemos ampliado el uso de estos frenos a los bancos de prueba de laboratorio con gran éxito”.