www.revista-fabricacion.com
28
'10
Written on Modified on
Verlinde equipa a NZ Steel
KraneQuip, distribuidor de Verlinde en Nueva Zelanda, se enfrentaba al reto de encontrar una solución racional para diseñar y construir una grúa puente con capacidad para 16 toneladas en un espacio limitado en las instalaciones de NZ Steel.
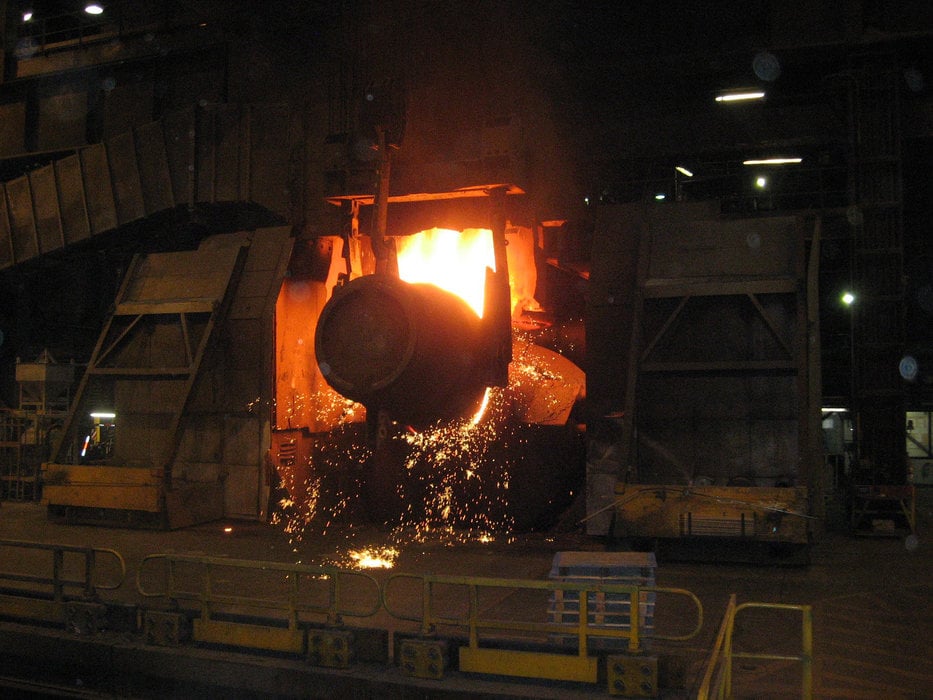
El primer problema era el poco espacio que había para colocar la grúa. "Fue un auténtico desafío hacerla caber en un espacio de sólo cuatro metros de ancho, sobre todo si tenemos en cuenta que la altura de elevación era de 30 metros", apunta el Sr. Van der Walt. "Normalmente, para esto se utiliza un polipasto de cable, pero para almacenar los 30 metros de cable que requería semejante altura de elevación era necesario un tambor muy voluminoso, prácticamente tan ancho como el espacio disponible". La carga puntual tenía que desplazarse de este a oeste por el raíl de la grúa, pero el polipasto de cable no era una opción viable debido a sus dimensiones. "Por eso nos decantamos por los polipastos de cadena. Sin embargo, el problema que tienen los cabrestantes de cadena es que no pasan de cinco toneladas, o 7,5 en nuestro caso, porque Verlinde, nuestro proveedor, podía fabricarlos de esta capacidad. En cualquier caso, faltaba mucho para llegar a las 16 toneladas que necesitábamos". Después de darle muchas vueltas, el equipo de KraneQuip propuso utilizar dos polipastos de cadena con una capacidad de diez toneladas cada uno. No obstante, en la práctica, tuvieron que combinar dos cables de cinco toneladas para conseguir diez toneladas. Luego, hubo que colocar dos de estos grupos de cables en el raíl de la grúa puente.
"Al cabo de sólo unas semanas, gracias a la potencia de este diseño, conseguimos instalar estos cabrestantes en el raíl de una grúa monorraíl para adaptarse a las dimensiones de carga puntual que habría que desplazar. Para ello, hubo que modificar el diseño de los cabios, jugando tan sólo con unos pocos milímetros".
La siguiente dificultad consistió en diseñar una grúa capaz de soportar 16 toneladas. El raíl recto estándar de mayor capacidad no era suficiente y un raíl de cajón se salía del presupuesto. Así pues, KraneQuip no tuvo más remedio que diseñar una grúa puente de raíl recto con unos refuerzos superiores y bridas en la parte inferior para sujetar la carga. Gracias a esta decisión, se pudieron recortar los plazos de ejecución y NZ Steel se ahorró el sobrecoste que habría acarreado la fabricación de un raíl de cajón.
Las dimensiones exteriores de los cárteres de las cadenas planteaban también un problema. Los dos polipastos, a pesar de estar perfectamente adaptados al diseño, no se podían acercar lo suficiente el uno al otro para satisfacer las distancias de acercamiento este y oeste. Por este motivo, hubo que modificar los dos cárteres de las cadenas centrales. "No se podía bajar más, porque no quedaba espacio. Por ello, decidimos tirar a lo ancho", comenta Cobus van der Walt. Entonces, surgió otro problema: conseguir que la cadena llenara toda la anchura de los cárteres en esta dirección. El equipo tuvo que colocar unas planchas deflectoras en el centro y abrir la garganta del cárter para que la cadena se pudiera repartir correctamente en el mismo. El primer intento no funcionó, pero, después de algunas modificaciones, se consiguió solucionar el problema.
Cuando se puso en servicio, se tuvieron que realizar varios ajustes para que los dos ganchos se trasladaran de manera idéntica y a la misma altura, y para que los conmutadores de los cabios se activaran simultáneamente. Topamos con muchas dificultades relacionadas con la velocidad de desplazamiento longitudinal, ya que la grúa sólo podía moverse muy despacio en todas las direcciones. Se utilizaron controles de velocidad variable para homogeneizar el funcionamiento. Sin embargo, en el desplazamiento longitudinal, se acumulaba mucha suciedad en los raíles y las ruedas resultaban demasiado anchas para aguantar toda la carga de la grúa más la carga máxima de trabajo. La potencia a baja velocidad a penas bastaba para mover la grúa, y la suciedad causaba obstrucciones. Al final, se decidió que la única solución era limpiar bien los restos de suciedad de los raíles antes cada uso.
"Para el equipo de KraneQuip, este proyecto representaba un reto sin precedentes y estamos muy orgullosos de haberlo podido superar", confiesa Cobus van der Walt. "Es extraordinario haber tenido la oportunidad de satisfacer las exigencias tan específicas que tenía NZ Steel, aunque a veces pareciese tarea imposible".