www.revista-fabricacion.com
21
'10
Written on Modified on
HMS Industrial Networks AB
Genzyme monitorea 50.000 puntos SCADA con Anybus Communicator
La compañía, líder mundial en biotecnología, está creando un nuevo sitio de producción de anticuerpos policlonales. Se trata de una innovadora facilidad de producción; el proceso ha sido automatizado lo máximo posible a fin de reducir el error humano en las etapas del proceso (separación, purificación, filtración, ultrafiltración, hemadsorción, etc.). Esto requiere la capacidad de interactuar con una cantidad de equipamiento de laboratorio muy diverso, el no fue originalmente diseñado para comunicarse con buses de campo. Genzyme utilizó cerca de treinta puertos de HMS Anybus Communicator, para permitir un consistente manejo SCADA entre todos los dispositivos en uso. Los beneficios se hacen ver tanto en la calidad como en los costos de producción.
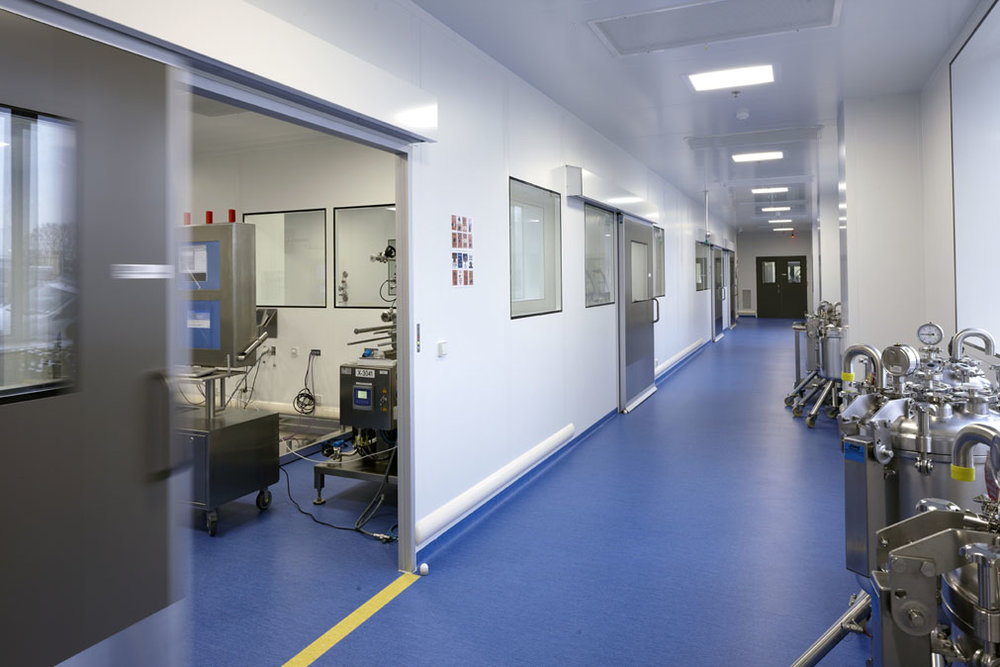
El espacio e bioproducción de Lyon se extiende en un área de 22.000 m2, y produce un inmunosupresor selectivo que se utiliza para prevenir y tratar el rechazo al nuevo órgano en los transplantes (Thymoglobulin®).Esta droga tambi´n se utiliza en hematología en los casos en que las células transplantadas reaccionan en contra de su huésped en los transplantes de médula ósea. Los agentes activos de esta droga son las inmunoglobinas anti-timocitos humanos, obtenidas de la purificación de un suero, que se utiliza como materia prima. La base inmunogénica consiste en timocitos (células Thymus), una fuente natural de células T. El desarrollo de este espacio implicó una inversión de 115 millones de euros.
»Actualmente, Genzyme utiliza métodos de producción de mano de obra intensiva en la locación de Sanofi Pasteur, Marcy. Con el nuevo lugar, esperamos optimizar el proceso para reducir el error humano al mínimo. El proceso, con muchas etapas secuenciales, incluye más de 780 etapas de producción. Hay muchas posibilidades de error. Automatizar un proceso como este ha requerido un trabajo muy cercano con el equipo involucrado a la hora de decidir cómo se debería comportar el sistema. Esto ha posibilitado evitar tener que repensar la completa ergonomía del edificio y del equipamiento de producción, sin dejar de ser una verdadera revolución por la forma en la que opera el proceso de producción. Para lograr esto, especificamos más de 4.000 parámetros y 13.000 alarmas, lo cual nos permite manejar cada etapa de producción,» explica Alexis Ducancel, oficial de sistemas automatizados de Genzyme.
Bioproducción: una serie de procesos complejos
A diferencia de la química tradicional, la producción basada en células vivas envuelve muchas etapas costosas, diferentes entre sí y complejas. El ciclo de producción de una proteína para recombinar requiere una infraestructura industrial que se sitúa a gran escala incluyendo etapas de producción durante muchos meses. Cada etapa está sujeta numerosos controles de calidad. Evaluaciones para asegurar la ausencia de virus y contaminantes se llevan a cabo también durante el ciclo de producción. Al final del proceso, además se evalúa la pureza y la acción de la proteína. La producción de esta droga implica muchas etapas complejas sumadas a una sucesión de tests técnicos y de calidad. El proceso de producción puede dividirse en cuatro etapas principales:
- La recolección de inmunoglobinas, la cual se realiza inyectando tejido humano en conejos.
- La purificación de las inmunoglobinas para remover las proteínas no deseadas (particularmente, anticuerpos antieritrocitos), por hemadsorción.
- La etapa de hematografía consiste en un intercambio de aniones a travás del uso de un intercambio iónico de resina. Se capturan las impurezas con la resina, si bien las inmunoglobinas, que no poseen carga negativa, se eluyen. Esta etapa se chequea utilizando espectrofotometría y electroforesis.
- La etapa de precipitación intenta eliminar las impurezas restantes. Las inmunoglobinas purificadas son pasteurizadas (60 °C por 10 horas). Esta solución se congela en seco antes de sellarse en viales.?
»En este proceso podemos, por ejemplo, programar los seteos de las centrifugadoras (velocidad, temperatura, tiempo de trabajo, etc.). Estos valores pueden cambiar en el SCADA para atender requerimientos específicos del momento de producción. Las lecturas se toman en todas las etapas y se envían al SCADA. Esto nos permite colocar procesos de trazabilidad muy precisos en el lugar. En particular, esto significa que la carga de trabajo para los equipos de control de calidad se reduce significativamente, lo cual es una ventaja en cuanto a costos,» agrega Alexis Ducancel.
La locación de Lyon, como la de MArcy, recibirá la aprobación de FDA y de AFFAPS.
»Lógicamente, elegimos HMS, porque sentimos que ninguna otra compañía tenía disponibles soluciones estándar para enviar información desde una cantidad de equipamientos diferentes que no necesariamente habían sido diseñados para conectarse con buses de campo. Tenemos 28 centrifugadoras, medidores de pH, balanzas, y demás. Los protocolos de interface varían: serial o ASCII, por ejemplo. Los 30 Anybus Communicator envían la data sobre Ethernet o Profibus a la central SCADA.»
Anybus Communicator: la solución para integrar equipamiento serial en una red de comunicación industrial
La serie de puertos Anybus Communicator para conectar con Fieldbus/Ethernet industrial hacen posible comunicar dispositivos en red que fueron desarrollados para ser utilizados en una red serial. El Anybus Communicator puede conectar la mayoría de los productos con interface serial RS-232/422/485 a Ethernet o fieldbus industrial. Realiza una conversión inteligente entre el protocolo de serie y la red de destino. Esta conversión se configura utilizando la herramienta software »ABC Config Tool». La configuración de la red, una vez completada, puede ser reutilizada por todas las redes soportadas por Communicator.
»Más allá de la calidad del producto, vimos que el soporte técnico estaba cada vez que lo necesitábamos,» concluye Alexis Ducancel.
Alrededor de cincuenta empleados se encuentran trabajando ahora en el lugar de producción de Genzyme, donde se llevan a cabo etapas iniciales de producción para validar el proceso completo. La producción completa debería comenzar a fines de 2011, una vez obtenidas las certificaciones AFSSAPS. El número total de staff de producción alcanzará entonces los 270 empleados.
Imagen 1:
El nuevo espacio de Genzyme para la producción de anticuerpos policlonales para transplantes y hematología ocupa 22.000 m2. La inversión fue de 115 millones de euros.
Imagen 2:
La gama Anybus Communicator permite a los datos seriales retroalimentarse en un sistema de control central.
Acerca de Genzyme
Genzyme nació en Cambridge, Massachusetts (Estados Unidos), en 1981, cuando sus fundadores apostaron a dar soluciones a pacientes afectados con graves enfermedades de las que no existía tratamiento alguno. Un acercamiento personalizado a la salud, sumado al deber de innovar, hizo una compañía de biotecnología de vanguardia reconocida en todo el mundo. Si bien la ayuda a pacientes afectados por raras enfermedades genéticas es aún una prioridad, Genzyme también provee tratamientos innovadores para ayudar a pacientes con problemas renales, cáncer o artritis, o a aquellos que requieran transplante o cirugía, además de su trabajo en campos tales como el diagnóstico. Genzyme, una compañía pionera de biotecnología es ahora una compañía diversificada que da empleo a 11.000 personas en todo el mundo.
»Actualmente, Genzyme utiliza métodos de producción de mano de obra intensiva en la locación de Sanofi Pasteur, Marcy. Con el nuevo lugar, esperamos optimizar el proceso para reducir el error humano al mínimo. El proceso, con muchas etapas secuenciales, incluye más de 780 etapas de producción. Hay muchas posibilidades de error. Automatizar un proceso como este ha requerido un trabajo muy cercano con el equipo involucrado a la hora de decidir cómo se debería comportar el sistema. Esto ha posibilitado evitar tener que repensar la completa ergonomía del edificio y del equipamiento de producción, sin dejar de ser una verdadera revolución por la forma en la que opera el proceso de producción. Para lograr esto, especificamos más de 4.000 parámetros y 13.000 alarmas, lo cual nos permite manejar cada etapa de producción,» explica Alexis Ducancel, oficial de sistemas automatizados de Genzyme.
Bioproducción: una serie de procesos complejos
A diferencia de la química tradicional, la producción basada en células vivas envuelve muchas etapas costosas, diferentes entre sí y complejas. El ciclo de producción de una proteína para recombinar requiere una infraestructura industrial que se sitúa a gran escala incluyendo etapas de producción durante muchos meses. Cada etapa está sujeta numerosos controles de calidad. Evaluaciones para asegurar la ausencia de virus y contaminantes se llevan a cabo también durante el ciclo de producción. Al final del proceso, además se evalúa la pureza y la acción de la proteína. La producción de esta droga implica muchas etapas complejas sumadas a una sucesión de tests técnicos y de calidad. El proceso de producción puede dividirse en cuatro etapas principales:
- La recolección de inmunoglobinas, la cual se realiza inyectando tejido humano en conejos.
- La purificación de las inmunoglobinas para remover las proteínas no deseadas (particularmente, anticuerpos antieritrocitos), por hemadsorción.
- La etapa de hematografía consiste en un intercambio de aniones a travás del uso de un intercambio iónico de resina. Se capturan las impurezas con la resina, si bien las inmunoglobinas, que no poseen carga negativa, se eluyen. Esta etapa se chequea utilizando espectrofotometría y electroforesis.
- La etapa de precipitación intenta eliminar las impurezas restantes. Las inmunoglobinas purificadas son pasteurizadas (60 °C por 10 horas). Esta solución se congela en seco antes de sellarse en viales.?
»En este proceso podemos, por ejemplo, programar los seteos de las centrifugadoras (velocidad, temperatura, tiempo de trabajo, etc.). Estos valores pueden cambiar en el SCADA para atender requerimientos específicos del momento de producción. Las lecturas se toman en todas las etapas y se envían al SCADA. Esto nos permite colocar procesos de trazabilidad muy precisos en el lugar. En particular, esto significa que la carga de trabajo para los equipos de control de calidad se reduce significativamente, lo cual es una ventaja en cuanto a costos,» agrega Alexis Ducancel.
La locación de Lyon, como la de MArcy, recibirá la aprobación de FDA y de AFFAPS.
»Lógicamente, elegimos HMS, porque sentimos que ninguna otra compañía tenía disponibles soluciones estándar para enviar información desde una cantidad de equipamientos diferentes que no necesariamente habían sido diseñados para conectarse con buses de campo. Tenemos 28 centrifugadoras, medidores de pH, balanzas, y demás. Los protocolos de interface varían: serial o ASCII, por ejemplo. Los 30 Anybus Communicator envían la data sobre Ethernet o Profibus a la central SCADA.»
Anybus Communicator: la solución para integrar equipamiento serial en una red de comunicación industrial
La serie de puertos Anybus Communicator para conectar con Fieldbus/Ethernet industrial hacen posible comunicar dispositivos en red que fueron desarrollados para ser utilizados en una red serial. El Anybus Communicator puede conectar la mayoría de los productos con interface serial RS-232/422/485 a Ethernet o fieldbus industrial. Realiza una conversión inteligente entre el protocolo de serie y la red de destino. Esta conversión se configura utilizando la herramienta software »ABC Config Tool». La configuración de la red, una vez completada, puede ser reutilizada por todas las redes soportadas por Communicator.
»Más allá de la calidad del producto, vimos que el soporte técnico estaba cada vez que lo necesitábamos,» concluye Alexis Ducancel.
Alrededor de cincuenta empleados se encuentran trabajando ahora en el lugar de producción de Genzyme, donde se llevan a cabo etapas iniciales de producción para validar el proceso completo. La producción completa debería comenzar a fines de 2011, una vez obtenidas las certificaciones AFSSAPS. El número total de staff de producción alcanzará entonces los 270 empleados.
Imagen 1:
El nuevo espacio de Genzyme para la producción de anticuerpos policlonales para transplantes y hematología ocupa 22.000 m2. La inversión fue de 115 millones de euros.
Imagen 2:
La gama Anybus Communicator permite a los datos seriales retroalimentarse en un sistema de control central.
Acerca de Genzyme
Genzyme nació en Cambridge, Massachusetts (Estados Unidos), en 1981, cuando sus fundadores apostaron a dar soluciones a pacientes afectados con graves enfermedades de las que no existía tratamiento alguno. Un acercamiento personalizado a la salud, sumado al deber de innovar, hizo una compañía de biotecnología de vanguardia reconocida en todo el mundo. Si bien la ayuda a pacientes afectados por raras enfermedades genéticas es aún una prioridad, Genzyme también provee tratamientos innovadores para ayudar a pacientes con problemas renales, cáncer o artritis, o a aquellos que requieran transplante o cirugía, además de su trabajo en campos tales como el diagnóstico. Genzyme, una compañía pionera de biotecnología es ahora una compañía diversificada que da empleo a 11.000 personas en todo el mundo.